Hygiene and Epidemic Prevention Bio-Security in the poultry farm
Section One: Providing and Ensuring a Biosecure Rearing Environment
Biosecurity emphasizes the role of environmental factors in maintaining flock health, and is fundamental to ensuring farming efficiency. Only by comprehensively implementing a biosecurity system and providing laying hens with an all-around biosecure living environment can we ensure the farming efficiency of the hens.
1. The Concept of Biosecurity
Biosecurity is a comprehensive disease control system, summarizing all effective safety measures that exclude communicable diseases, parasites, and pests. By controlling pathogenic microorganisms, insects, wild birds, and rodents, and ensuring chickens have good antibody levels, under good breeding management and scientific nutritional supply conditions, chickens can reach their maximum production potential.
Currently, epidemics severely trouble the healthy development of laying hens, with some even causing panic in many countries and regions. The proposal of biosecurity is related to the development of laying hen production and technological levels. Through the effective implementation of biosecurity, diseases can be kept away from chicken farms, or if pathogens exist, this system will be able to eliminate them, or at least reduce their numbers and density, ensuring good production results and economic benefits in poultry farming, and guaranteeing that the final products have good food safety, market competitiveness, and social recognition.
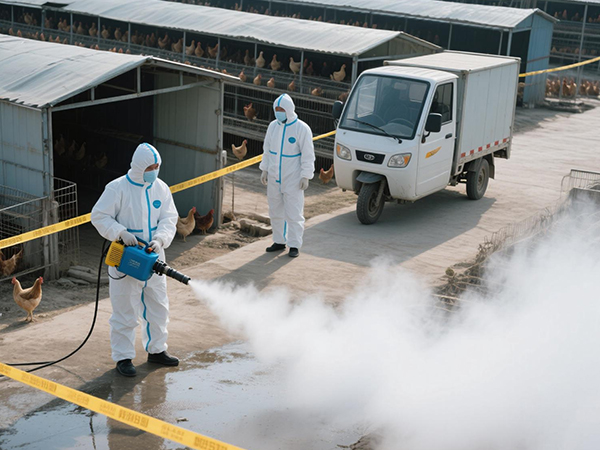
2. The Essence of Biosecurity
Establishing a biosecurity system for laying hen farms is a guarantee for producing harmless and safe egg products. The essence of biosecurity refers to veterinary health management of the environment, flocks, and personnel. Biosecurity includes three parts: isolation, traffic control, hygiene, and disinfection. Around these three major parts, the biosecurity system can be divided into three different management levels: architectural biosecurity measures, conceptual biosecurity measures, operational biosecurity measures. Comprehensive measures are taken from establishing a biologically safe isolation system, strictly enforcing disinfection measures, ensuring safety in immunization and prevention work, strengthening the hygiene and safety management of inputs, and the harmless treatment of chicken farm waste.
(1) Architectural Biosecurity Measures – Scientific and Reasonable Isolation Zones
- Scientific Location Selection and Zoning Isolation of Farms Good transportation facilitates the input of raw materials and output of products, but farms should not be close to villages and main roads because of frequent human movement and numerous passing vehicles that easily spread diseases. Chicken farms should be at least 1 kilometer away from villages and more than 500 meters from main roads. This ensures convenient transportation while avoiding stress effects on chickens from uncertain factors in villages and roads, and also reduces the entry of certain pathogenic microorganisms. Farms, hatcheries, and slaughterhouses should have isolation zones according to the generations and division of production in chicken farms.
- Reforming Production Methods Gradually transform simple small-scale farmer production methods where humans and chickens coexist into modernized, automated medium and small-sized chicken farms, using advanced scientific breeding methods to ensure chickens live in optimal environmental conditions. High-density chicken farms not only have large numbers of chickens, technicians, feed transporters, and poultry carriers operating in the area but can also cause severe pollution leading to more serious harm events such as avian influenza incidents. Therefore, it is necessary to reasonably plan the density of chicken coops, keeping reasonable distances and densities between farms and between coops. The size and structure of chicken farms should also be flexibly managed based on specific conditions. Overly large chicken farms are difficult to maintain high levels of production efficiency. Therefore, in general, it is recommended to develop medium and small-sized chicken farms. Of course, if there is sufficient funding and technical support, large chicken farms can also be built. Reasonably divide functional units from the perspective of human and chicken health care, according to the needs of each production stage, reasonably divide functional areas. Units or areas that can be isolated and locked down should be provided to facilitate emergency isolation when problems occur. First, the chicken farm should have walls or fences for zoning isolation, generally declining visits to prevent pathogen invasion and avoid cross-infection, keeping social epidemics out; second, according to the different nature of land use, strictly divide the farm area into production and living areas; according to the different nature of road use, divide them into production roads and sewage paths. The production area and living area must be strictly separated by partition walls or buildings, and a disinfection room and disinfection pool must be set up between the production area and living area. Entry and exit from the production area and living area must pass through the disinfection room and step on the disinfection pool.
- Chicken Farm Personnel Stay Inside, Separating Humans and Chickens It is advocated that breeding personnel do not raise poultry at home and prohibit contact with other birds to prevent breeding personnel from becoming vectors of chicken infectious diseases. Preferably use married couples as workers, advocating that they live inside the farm, providing couple dormitories, which can reduce the frequency of workers going out, thereby reducing contact with outsiders, and better protecting the safety of the chicken farm. (2) Conceptual Biosecurity Measures – Systems and Plans Formulated According to Safety Concepts At the entrance of the farm area, there should be a disinfection room and disinfection pool equipped with disinfection tools and prominent warning signs. Inside the disinfection room:
- Purify the environment, eliminate pathogens, interrupt transmission chains Equip with UV lamps, disinfection sprayers, and rubber boots. The disinfection pool should have appropriate depth and long-term presence of disinfectant water. Warning signs should read “Breeding Area, No Entry” and hang prominently at the entrance gate or on both sides of the gate. According to the breeding scale, set up settling ponds, temporary manure stacking areas, and dead chicken processing zones. Sewage settling ponds and manure stacking areas should be located far from the production area, downwind, and hidden places to prevent unnecessary pollution within the farm area. Dead Cleanliness, separation of clean and dirty pathways, separate routes for transporting chicks, feed, personnel, and chicken manure. Roads inside the farm area and at the main gate must be hardened for easy disinfection and epidemic prevention; drainage systems should have reasonable slopes based on terrain to ensure smooth sewage discharge and prevent sewage from flowing outside the drainage system and sewage paths; manure trucks entering the farm must strictly disinfect the wheels, prevent spillage during loading, cover tightly with tarpaulin after loading to prevent environmental pollution. Require no dust, no cobwebs, no feces, no feathers, no beetles, no cracks, no rat holes inside the chicken coop, thoroughly wash and disinfect 3-5 times. Isolation and bathing system for production personnel; strict gatekeeper disinfection system; disinfection of hands, shoes, clothes, tools, vehicles, prohibition of external vehicles from entering; winter insulation and sealing measures for car disinfection rooms, adding salt to winter disinfection pools to prevent freezing; bedding disinfection to prevent mold.
- Strengthen Disinfection (1) Environmental Sanitation Disinfection Establish biological epidemic prevention barriers and protective forests inside and outside the farm environment. Based on climatic conditions, thoroughly disinfect the main roads inside and outside the chicken farm every 5 days. Regularly clean the environment and roads of the chicken farm. Use 0.3% peracetic acid to disinfect sewage pools, sewer outlets, and manure cleaning outlets monthly inside the farm. Timely clear weeds, tidy the ground inside the farm, remove low-lying water accumulation, dredge waterways, and do well in sewage and rainwater discharge within the farm area to eliminate conditions for the survival of pathogenic microorganisms. Turn over the topsoil in the environment once a year to reduce organic matter in the environment, which is conducive to environmental disinfection. (2) Personnel and Vehicle Disinfection 1 Disinfection of main entrances and farm areas. Main entrances must have disinfection pools, with the length of the disinfection pool being two circumferences of the vehicle wheels or more. It’s best to have a roof above the disinfection pool to prevent sun exposure and rain. The disinfectant solution uses 0.3% peracetic acid, replaced three times a week. 2 Usually, good environmental sanitation work in the farm area should be maintained, often using high-pressure water flushing. Each chicken coop door should also have a foot disinfection trough, and the disinfectant solution should be changed at least twice a week. When entering and exiting the chicken coop, wear different dedicated rubber long boots, and step on the disinfection trough for disinfection before entering the chicken coop. Wash the removed boots and soak them in another disinfection trough, perform hand disinfection, and wear disinfected work clothes and caps to enter the chicken coop. 3 At the entrance of the production area, the disinfection changing room is equipped with UV lamps, and production personnel undergo 2-3 minutes of disinfection when passing through. 4 Under normal circumstances, visits to the farm are declined. Higher-level leaders inspecting work or those who must visit, upon approval, like the production area staff, must undergo strict disinfection. Personnel entering the production area of the chicken farm, especially those directly contacting the flock, must follow this procedure to disinfect before entering: undress → bathe → change clothes and shoes → start working. 5 Work clothes should be washed every 3 days and exposed to sunlight. Breeders should change out of their work clothes, wash and disinfect them before leaving during shift changes. Work clothes and hats should be hung in the changing room after work every day and disinfected under sufficiently intense UV lights. 6 Technicians checking and patrolling chicken coops or production areas can easily become vectors for disease transmission. Technicians should pay more attention to their own disinfection. Especially those responsible for immunization work, after completing the immunization of a batch of chickens, they must wash their hands with disinfectant, and their work clothes should be soaked in disinfectant for 10 minutes and then exposed to sunlight for disinfection. 7 Breeding personnel should stay on duty, not switch coops, and all tools and equipment must be used exclusively for designated coops. 8 After each vaccine immunization, personnel require washing and disinfection of clothes, shoes, and hats. (3) Disinfection of Chicken Coops Dry, disinfect, dry again, disinfect again. Comprehensive disinfection of chicken coops should be carried out in a specific order: emptying the chicken coop, cleaning, washing, disinfecting. 1 Emptying the chicken coop. The principle of renewing the flock is the “all-in all-out” system, trying to clear all chickens in a short period. 2 Cleaning. After the chicken coop is emptied, remove the residue from drinkers and feed troughs, sweep dust from fans, vents, ceilings, beams, hangers, walls, and then remove all bedding and manure. To prevent dust from flying, sprinkle water or disinfectant beforehand, and centrally handle the removed manure and dust. 3 Washing. After cleaning, use power sprayers or high-pressure water guns for washing, following the order from top to bottom, inside to outside. Dirtier areas can be manually scraped beforehand, paying attention to corners, gaps, and the back of facilities, ensuring no blind spots and truly achieving cleanliness. 4 Disinfecting the chicken coop. After thorough washing and maintenance checks, disinfection can proceed. Fumigation disinfection commonly uses formalin with potassium permanganate, etc. This method is comprehensive and convenient but requires the chicken coop to be sealed. Since formaldehyde gas has weak penetration ability, before fumigation, disinfection objects should be scattered, and water should be sprinkled inside the coop to maintain relative humidity above 70%, and temperature above 18°C. Generally, use 50 ml of formalin, 12.5 ml of water, and 25 grams of potassium permanganate (or equivalent quicklime) per cubic meter of disinfection space. Open windows and ventilate after 12-24 hours of disinfection; if urgently needed, ammonia can neutralize formaldehyde gas. 5 Chicks can enter the empty coop after 15-20 days. (4) Disinfection of Equipment 1 Egg boxes, chick boxes, and chicken cages frequently entering and exiting the chicken coop must undergo strict disinfection. All transport tools should be scrubbed clean beforehand, dried, and then fumigated for disinfection, ready for use. 2 Injection equipment, needles, etc., for immunization should be cleaned and boiled for disinfection before each use. Laboratory equipment and items should be disinfected after each use. 3 Drinking vessels, feed troughs, feed buckets, water tanks, and other equipment should be cleaned and disinfected weekly. 4 After daily removal of chicken manure, all used equipment must be cleaned, and equipment inside and outside the coop should be strictly separated.
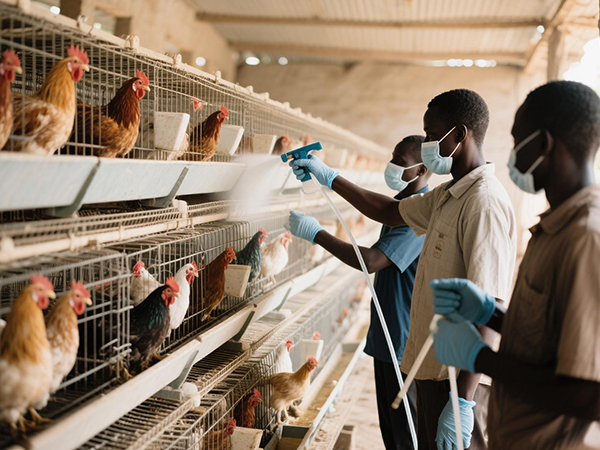
(5) Water Disinfection 1 Extremely beneficial for preventing viral and bacterial diseases, especially respiratory diseases. 2 Water should be clean, nontoxic, free of pathogens, and meet human drinking water quality standards. 3 Unless other incompatible drugs are added to the water or ongoing water vaccination is taking place, water disinfection should not be interrupted throughout the entire breeding cycle. 4 Water disinfection is also effective in preventing water scale deposits in water troughs. (6) Live Chicken Disinfection Live chicken disinfection refers to regularly spraying effective disinfectants on the chicken house environment and the surface of live chickens during the entire rearing period from when chickens enter the coop until culling. This kills airborne and surface-bound pathogens on the chickens, cleans the chicken’s surface, settles floating dust inside the coop, suppresses ammonia generation, and lowers ammonia concentration. In summer, it also helps cool the chickens. Generally, live chicken disinfection can be implemented starting from 10 days of age. During the brooding period, it should be done once a week; during the growing period, twice a week; and for adult chickens, every three days, or daily during outbreaks. The ideal spray droplet diameter is 80-100 microns, with a spray distance of 1 meter. The temperature inside the coop should be raised by 3-4°C higher than usual during spraying, and in winter, the disinfectant solution should be heated to room temperature. The amount of disinfectant solution used is 60-240 milliliters per cubic meter, making the ground, walls, ceiling uniformly moist and the chicken’s surface slightly wet. It is best to change the disinfectant every 3-4 weeks. Commonly used live chicken disinfectants include 0.15% peracetic acid. Before each live chicken disinfection, use a long broom to sweep away dust and spider webs inside the coop, then proceed with the live chicken disinfection.
(7) Disinfection of Breeding Eggs and Hatchery Workshop Collected breeding eggs should go through fumigation disinfection before entering the warehouse or incubation room. Collect breeding eggs promptly; the earlier the disinfection, the better, ideally within 2 hours after collection. Factors affecting the disinfection effectiveness of breeding eggs include dosage of the disinfectant, environmental temperature and humidity, disinfection time, and ventilation conditions. Methods for breeding egg disinfection. Liquid disinfectants can be sprayed or used for soaking; the required droplet diameter for spraying is 50 microns. However, the most effective method is still formaldehyde fumigation. Note that fumigation is prohibited for eggs 24-96 hours after setting, as it can harm embryo development. Chick disinfection. Generally, chicks are not subjected to fumigation disinfection, but when outbreaks of omphalitis, white diarrhea, paratyphoid, or severe contamination of the chicken farm occur, fumigation should be performed on the chicks. After formaldehyde fumigation, the chick’s fluff will turn dark brown. Disinfection of the hatchery workshop, incubators, and hatching machines. After each batch of chicks hatches, first thoroughly clean the machines with detergent, then fumigate with formaldehyde. Place enamel or ceramic containers filled with formaldehyde inside the machine to be fumigated, then pour in potassium permanganate. Regularly add disinfectants to the drain openings in the hatchery, and regularly spray disinfectants indoors and outdoors. Very dirty breeding eggs should be gently wiped with a disinfectant. Wash hands with detergent before collecting breeding eggs.
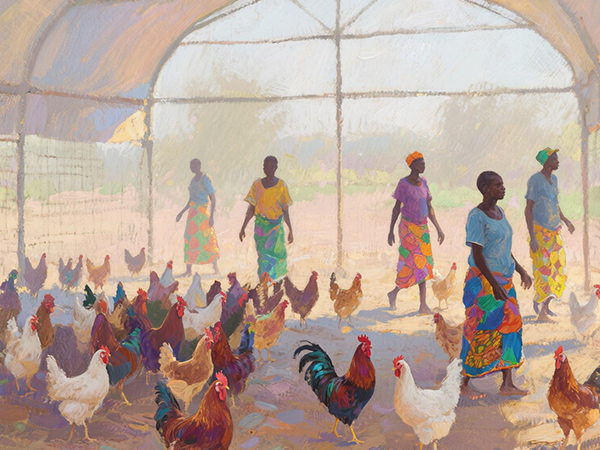
(8) Disinfection of Manure and Dead Chickens Daily chicken manure should be promptly removed, piled at the manure field, and transported off-site via manure trucks or fermented using biological fermentation. Tools, workwear, and other items used for handling chicken manure should also be cleaned and disinfected. Dead chickens should undergo high-temperature treatment or deep burial fermentation.
(3) Operational Biosecurity Measures – Daily Work Details Formulated Based on Safety Concepts
- Careful Feeding, Reducing Stress Every occurrence of disease inevitably involves improper feeding management. Eighty percent of disease issues in laying hen production are caused by inappropriate feed, ventilation, insulation, lighting, and water supply. Prevention is more important than cure. Reducing stress and enhancing the comprehensive immunity of the flock are among the important means to improve production performance.
- All-In All-Out Feeding System Modern laying hen production almost universally adopts the “all-in all-out” feeding system, meaning that the same batch and age of laying hens are reared in one chicken house, all chicks are raised under the same conditions, and transferred or culled on the same day. This management system is simple and practical with many advantages: it is convenient to manage during the breeding period, allowing for the use of identical technical measures and management methods, easy temperature control, facilitating mechanical operations, and helping maintain the hygiene of the chicken house and the health of the flock. After laying hens reach 500 days of age and are culled, the chicken house and its equipment undergo comprehensive and thorough cleaning, flushing, and fumigation disinfection. This not only cuts off the cycle of infection but also results in more uniform egg production, less feed consumption, and lower mortality rates compared to raising several different age groups of chickens in the same house.